Система контроля эффективности производства
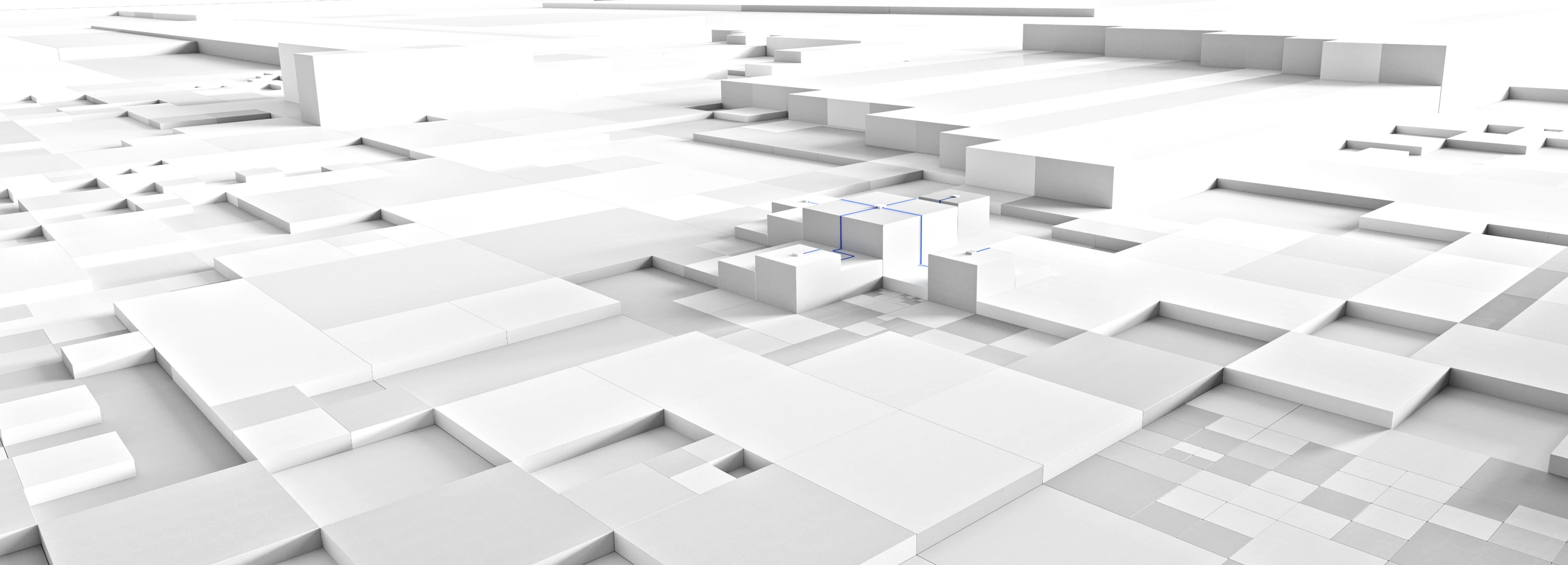





Обеспечивает контроль производства по методике
Overall Equipment Effectiveness (OEE).
Оценка Общей Эффективности Оборудования (ОЭО) — это комплексный контроль производства на основе трёх ключевых составляющих: простои, производительность и качество.
Позволяет в короткие сроки и с минимальными затратами наладить централизованный объективный мониторинг эффективности на предприятиях с большим количеством разрозненных обрабатывающих центров – станков, агрегатов и производственных линий.
Принципы построения системы
Система строится на принципах максимальной объективности и непрерывности контроля, адаптируется к специфике предприятия и отдельных подразделений.
Приоритетное использование автоматического сбора данных
Исключает «человеческий фактор» - сокрытие или перераспределении потерь производства. Для сбора информации, которая недоступна для автоматического сбора, система предоставляет формы ручного ввода со строгим регламентом заполнения.
Глубокая адаптация системы к специфике производства
Для каждого агрегата могут быть применены специальные алгоритмы сбора и учета данных. Доступ сотрудников к функциям контроля и редактирования данных, а также эскалации оповещений настраивается с учетом особенностей организационной структуры.
Гибкая интеграция с потребителями данных
Система может являться источником объективных данных о результатах производства (объемах производства, простоях и качестве продукции) для систем корпоративного уровня (например, системы управления предприятием – ERP), чем значительно повышает эффективность их применения.
Гибкая интеграция с источниками данных
Система позволяет настроить сбор из любых доступных источников данных (контроллеров, SCADA, измерителей, датчиков, весов, сканеров).
Для повышения достоверности контроля и исключения двойного ввода реализуется необходимый обмен данными со смежными АС.
Показатели эффективности
В базовые настройки входит набор типовых универсальных KPI. Он может свободно дополнятся и расширятся с учетом специфики производства.
Коэффициент OEE
Понятный, надежный и удобный KPI для количественной оценки состояния производства. Достоинства ОЭО сделали его наиболее популярным индикатором эффективности подразделений, персонала, предприятия.
ОЭО = A (доступность) × P (производительность) × Q (качество)
Доступность (Availability, A) — отклонение длительности простоев от плановых/нормальных значений.
Производительность (Performance, P) — отклонение объема производства от плановых/нормальных значений.
Качество (Quality, Q) — доля некачественной продукции.
Коэффициент расхода сырья (КРС)
Отношение единицы израсходованного сырья к выходу готовой продукции – важнейший показатель перерабатывающего производства, характеризующий как эффективность производства и качество сырья.
Среднее время межремонтного периода (MTBF)
Характеризует состояние оборудования и качество технического обслуживания.
Коэффициент технической готовности (КТГ)
Отношение времени исправного состояния оборудовании к общему времени. Важнейший коэффициент для общей оценки качества технического обслуживания и общего состояния парка оборудования.
Среднее время ремонта (MTTR)
Характеризует скорости реакции служб ТОиР и устранения неисправностей.
Основные функции
Система обеспечивает выполнение следующих основных функций
Сбор и первичная обработка данных
-
Настройка сбора данных из различных источников.
-
Настройка алгоритмов автоматического определения событий на основе произвольного сочетания первичных параметров.
-
Преобразование данных для долговременного хранения.
-
Контроль состояния сбора данных.
Контроль простоев
-
Полностью автоматическая или автоматизированная фиксация простоев и событий снижения производительности.
-
Автоматизированная классификация простоев и событий снижения производительности.
-
Управление нормативами простоев и учетом графиков плановых простоев.
Контроль производительности
-
Полностью автоматическая или автоматизированная фиксация входящего объема сырья и объема готовой продукции.
-
Управление нормативами расхода сырья при производстве различных видов продукции.
Контроль технологии и качества
-
Полностью автоматическая или автоматизированная фиксация технологических параметров и свойств продукции.
-
Средства ввода или импорта результатов контроля качества.
-
Управление нормативами технологических параметров и параметров контроля качества.
Оперативный мониторинг производства
-
Предоставление WEB интерфейса с возможностью контроля текущей ситуации в режиме онлайн из любой точки сети.
-
Предоставление трех уровней детализации данных – уровень предприятия, уровень производственного подразделения, уровень агрегата.
-
Автоматическое определение отклонений от плановых/нормальных значений контролируемых параметров и оповещения персонала с настройкой уровней эскалации оповещения.
Хранение и анализ данных
-
Организация долговременного хранения данных.
-
Предоставление средств ретроспективного анализа с настраиваемыми параметрами выборки данных.
Формирование отчетности
-
Формирование типовых отчетных форм для систематического контроля с возможностью настройки типовых периодов времени и направлений контроля.
-
Формирование специализированных отчетных форм для быстрого анализа отдельных аспектов производства в соответствии со спецификой.





Эффективность
Внедрение системы обеспечивает существенный комплексный эффект.
-
Повышение качества продукции за счет непрерывного контроля параметров, анализ, выявления и устранения источников нарушений
-
Повышение производительности на основе быстрого реагирования служб ТОиР, оперативного и точного принятия решений.
-
Снижение стоимости учета путем автоматизации рутинной документации и выгрузки данных в смежные системы.
-
Рост трудовой дисциплины за счет устранения возможности сокрытия нарушений и развития системы мотивации.
Преимущества
Система максимально использует данных объективного контроля – руководители видят ситуацию без искажений и могут провести ретроспективный анализ.
Система является "облегченной" альтернативой MES – реализует важнейшие функции MES при минимальных затратах.
Система автоматизирует передачу в ERP данных о фактическом производстве – формируемая отчетность обновляется в режиме близком к реальному времени.
При наличии базовой инфраструктуры, решение требует минимальных временных затрат на адаптацию и организацию сбора данных.
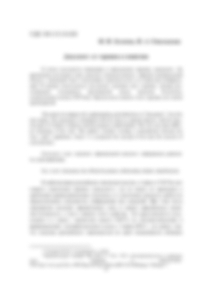
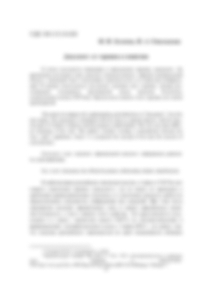