Система оперативного планирования производства
Обеспечивает расчет согласованных детальных графиков производства на агрегатах технологического цикла с учетом требований к срокам производства заказов, доступности ресурсов, правил монтажности и технологических ограничений.
Позволяет формировать графики работы оборудования и проводить их настройку на горизонте нескольких суток — оперативно компенсировать возникающие отклонения с соответствующей перестройкой расписаний смежных агрегатов в режиме реального времени.
Система нацелена на выполнение календарного плана производства заказов, распределенных по суточным квотам агрегатов. Одной из важнейших задач оперативного планирования является своевременный учет и компенсация отклонений от запланированных параметров процесса, учета поломок оборудования, отклонений от сроков на предыдущих переделах, доступности транспорта, фактической годности продукции.
Особенности оперативного планирования металлургического производства
Правила монтажности
Графикование металлургических агрегатов основано на учете большого количества правил – обязательных или рекомендованных последовательностей единиц обрабатываемого материала. В случае значительного количества агрегатов задача корректного учета всех правил с учетом последовательного перемещения и доступности полуфабрикатов на следующих стадиях является весьма сложной.
Зачастую правила монтажности не могут быть соблюдены в полном объеме на доступном сортаменте, что требует принятия экспертных решений, индивидуальных для каждой конкретной ситуации.
Жесткие требования к согласованию смежных участков
Во многих случаях необходимо строгое согласование графиков десятков агрегатов с обеспечением строгих требований к синхронизации, межоперационным паузам, перестройкам сортамента. Типичный пример – цеха выплавки и разливки металла, где полуфабрикаты должны оперативно перерабатываться на каждой следующей стадии. При этом длительности отдельных операций могут отклоняться по различным технологическим причинам, поэтому должна обеспечиваться возможность быстрого реагирования на отклонения.
Принципы реализации
Инструменты системы адаптированы к условиям металлургического производства. Система оперативного планирования обеспечивает первичное формирование и последующую автоматизированное адаптацию графиков производства агрегатов, предоставляя специалистам планово-распределительных служб необходимые инструменты.
Гибкий учет производственно логистики каждого объекта
В идентичных типах производства каждый производственный объект может обладать уникальными особенностями в части движения материальных потоков, набора агрегатов, их технологическими возможностями.
Формируемый комплект инструментов управления обеспечивает необходимую точность отражения особенностей. При этом поддерживается необходимая гибкость в настройке детальных графиков и свобода действий диспетчеров и операторов, которые необходимы для эффективного управления технологическим процессом.
Учет всех значимых операций
Используется принцип учета всех значимых операций, влияющих на темп изготовления полуфабрикатов и продукции. В случае необходимости вводятся дополнительные формы управления, например, инструменты графикования ручных операций с учетом текущего наличия персонала на участках.
Поддержка различных видов графикования агрегатов
Система позволяет устанавливать необходимый формат графикования в зависимости от особенностей каждого агрегата, темпов производства, учета фактических параметров и других факторов. Реализованы различные виды контактных графиков для управления группами агрегатов, графики отдельных агрегатов с различными формами правил смены сортамента и монтажности, сменные и суточные задания.
Графикование комплектации и отгрузки
Высокие темпы и объемы производства требуют особого внимания к обеспечению ритмичной комплектации и отгрузки полуфабрикатов и готовой продукции. Система учитывает правила и особенности комплектования различными видами металлопродукции графикования. Обеспечивает быстрое и безошибочное управление процессами.
Особенности назначения / переназначения
Огромная вариативность параметров металлургической продукции существенно затрудняет процессы привязки той или иной единицы к конкретному заказу. В системе реализованы необходимые элементы гибкого управления переназначениями с автоматическим контролем корректности операций и баланса материалов.
Быстрый доступ к дополнительной информации
Каждый элемент в графике производства отображается в привязке к конкретным заказам с полным набором параметров и требований. Это поддерживает ключевую концепцию системы – учет потребностей клиентов на всех стадиях производства и управление процессами, нацеленное на выполнение заказов.
Система отслеживает не только ход выполнения каждого заказа, но и контролирует его соответствие предъявляемым требованиям. Возникающие в производстве остатки учитываются как «свободное» наличие и приоритетным образом используются при выполнении текущих или вновь поступающих заказов.
Основные функции
Детальные графики производства рассчитываются на основе планового наполнения производственными заказами соответствующих квот календарного плана.
Ключевые параметры оперативного планирования
Гранулярность / шаг — реальное время.
Горизонт — 1-7 суток.
Детальность — каждая учетная единица полуфабриката или продукции.
Частота перепланирования / обновления — непрерывная актуализация (типовая периодичность 1 раз в минуту).
Взаимодействие со смежными системами
Выполняется загрузка планового распределения заказов в квотах календарного плана на несколько ближайших суток. Использование нескольких суток позволяет более гибко формировать графики агрегатов со строгими правилами монтажности и формирования последовательностей в заданиях.
Между периодами расчета следующих версий календарного плана оперативные графики производства непрерывно обновляются на основе отслеживания данных о фактическом производстве.
Расчет детальных (оперативных) графиков производства и отгрузки
Первичный расчет оперативного плана для каждого объекта планирования выполняется с учетом индивидуального комплекса правил и ограничений. Соответствующие основные данные настраиваются в системе управления НСИ. В системе реализовано большое количество типовых настроек для различных форм графиков и типов объектов планирования. Ключевой характеристикой расчета является высокая скорость, необходимая для постоянной актуализации графика.
Управление детальными (оперативными) графиками производства и отгрузки
Система предоставляет диспетчерским службам инструменты автоматизированной корректировки и управления графиками. В случае внесения ручных корректировок применяются функции автоматического выявления нарушений правил графикования с информированием пользователей. Реализован строгий контроль и протоколирование всех действий, информирование операторов о допускаемых отклонениях.
Управление переназначениями
Система предоставляет развитые инструменты оперативного назначения и переназначения полуфабрикатов и готовой продукции со сквозным учетом требований конкретных клиентских заказов. Выполняется автоматический контроль всех значимых параметров материалов, выполняется автоматический подбор вариантов заказов для единиц учета или наоборот — единиц учета для заказов.
Эффективность
В составе комплекса интегрированного планирования тактический уровень детального графикования операций обеспечивает гибкое выполнение стратегических задач, поставленных на уровне объемного и оперативного планирования. Автоматизированные инструменты существенно облегчают процесс управления и кардинально снижают количество ошибок и связанных с ними потерь.
Эффективность инструментов основана на обеспечении необходимой гибкости оперативного управления при строгом контроле сквозного выполнения плановых операций для достижения максимальной эффективности работы всего предприятия в целом.
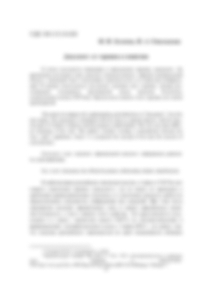
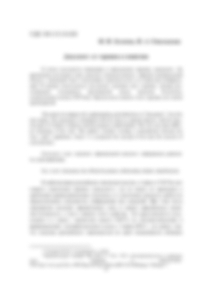